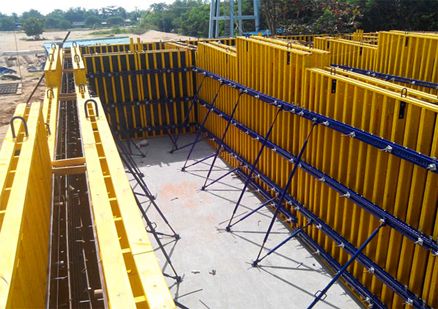
At Zolo, we have invested time and effort into creating superior and reliable wall formwork systems. Through our products, we aim to provide formwork solutions as well as bracing and support systems that enable developers to complete a wide range of construction projects quickly, safely and efficiently. We offer a comprehensive range of heavy-duty and light-duty wall formwork systems for the development of concrete walls of all shapes and sizes. We also offer formwork solutions for curved walls and columns, making it easy to build infrastructure and construction projects with unique geometries. Whatever formwork you need to build walls with a consistent, high-quality concrete finish, you'll find it at Zolo.
What is a wall formwork?
The wall formwork is a type of formwork used to construct walls in numerous types of construction applications. Wall formwork can be made of timber, steel, aluminum, or other materials.
What is the maximum permissible filling height of a wall formwork?
The maximum height of a concrete wall cast using industrial formwork depends on many factors:
Maximum design pressure: Each panel type is designed for a maximum compressive capacity. Industrial formwork is usually designed for a maximum pressure of between 40 and 80 kN/m².
The fluidity of the concrete used: The more fluid the concrete, the greater the pressure. Special attention must be paid when using self-compacting concrete "SCC". (See question 7).
Filling time: The faster the concrete is filled, the greater the pressure on the formwork. When using more fluid concrete at higher heights, the filling speed must be kept lower, which the formwork supplier must indicate in a dedicated form.
External temperature: This affects the curing of the concrete: The lower the temperature, the longer the curing time and the greater the load on the formwork.
Another factor to be considered is the vibration of the concrete, which makes the concrete flow, maintains pressure and delays its curing. Deep vibrations can put a lot of load on the formwork. For example, at heights above 6 meters, it is more difficult to vibrate the concrete using the pin vibrators usually used on site. Therefore, when using external wall-mounted vibrators, their positioning must be studied correctly.
Which factors during the use of wall forms have the greatest impact on the finish of the concrete?
Sometimes, stains or "pinholes" of varying shades may appear in the concrete finish once the panels have been stripped. This can have several reasons. Stains are usually caused by the use of low-quality or inappropriate release agents, which react with the concrete in certain areas. Pinholes or cracks are mainly caused by poorly executed vibration or poor concrete selection. Both of these can also be caused by improper formwork cleaning.
Generally speaking, for architectural or eye-catching finishes, phenolic facing panels are recommended because they have a very low surface porosity and therefore a glossy surface.
Can vertical formwork be handled manually?
Wall formwork is divided into three main categories: manual formwork, lightweight formwork and solid formwork.
Light formwork: These are metal frame panels that usually weigh no more than 20 kg/m². These panels are easy to handle, but have the disadvantage of having a lower resistance to concrete pressure (about 40kN/m²) and a shorter service life. They are mainly used in countries with less crane use or for construction solutions where cranes are not available.
Manual formwork: These panels are somewhere between solid and lightweight panels, combining the characteristics of both, usually weighing between 30 and 60 kg/m², with manual portability and usually resisting pressures between 40 and 80 kN/m².
Solid formwork: "Solid" panels are designed to withstand heavy loads and can usually only be handled with mechanical lifting equipment. The weight of these panels usually exceeds 60 kg/m².
What is the standard vertical formwork equipment for a construction site?
When planning a new construction project, a well-known question often arises: How many square meters of formwork do I need to implement my project?
It is difficult (or even impossible) to define a standard equipment that is suitable for each construction site. Each project is unique in its own way. However, it is possible to define the criteria for the best equipment for each construction site:
Number of operators: First of all, it is very important to determine the number of workers and teams that handle the formwork. On large construction sites, several groups of workers are hired at the same time, each of which requires a formwork team.
Number of cranes: The number of formwork equipment should not exceed the number of cranes on site. Sometimes, the production speed may be reduced due to the fact that the number of formwork equipment exceeds the handling capacity on site.
Production times on site: Obviously, for the construction of walls, it is necessary to adhere to times that can be managed without problems under standard conditions. However, it is true that on some construction sites, the times required by the developer mean that these deadlines need to be shortened, so the number of workers and formwork equipment on site must be increased.